Hey there, facility managers, safety pros, and asset tracking warriors! Aluminum tags – those tough little metal workhorses – seem straightforward, right? Just slap 'em on something and forget about 'em. But hold your horses! That kind of thinking can lead to some seriously expensive headaches, safety risks, or just plain wasted effort down the line.
As someone knee-deep in industrial labeling day in and day out, I see the same aluminum tags mistakes crop up way too often. These tags are built tough for harsh environments – think chemical plants, manufacturing floors, heavy machinery, or out in the unforgiving weather. But if you don't use 'em right, you're throwing money away and potentially creating bigger problems. Let's break down the five most common slip-ups and, more importantly, how to dodge 'em like a pro.
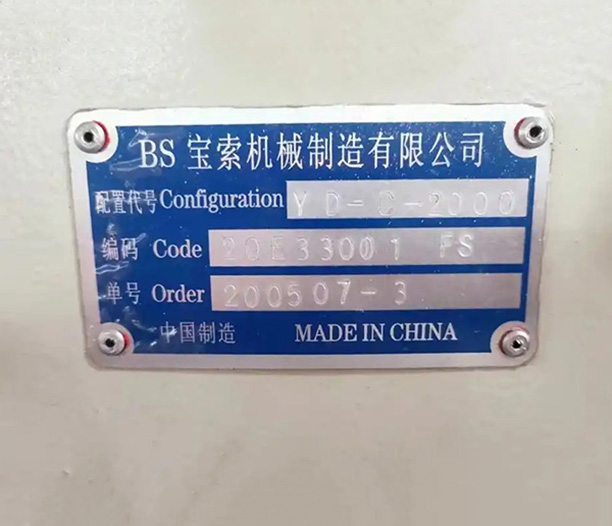
Mistake #1: Choosing the Wrong Aluminum Alloy (It's Not All the Same!)
This is the granddaddy of mistakes. Assuming all aluminum tags are created equal is like assuming every wrench in your toolbox does the same job. Big mistake!
- The Problem: Different environments demand different alloys. Using a soft, commercially pure aluminum tag (like 1100) in a highly corrosive chemical plant? That tag's gonna pit, corrode, and become unreadable faster than you can say "replacement budget." Conversely, using a super-hard marine-grade alloy (like 5052) for simple indoor asset tagging is serious overkill – and a waste of your budget.
- The Fix: KNOW YOUR ENVIRONMENT! Match the alloy to the challenge:Mild Indoor/General Use: 3003 alloy is a great, cost-effective all-rounder.Harsh Chemicals/Cleaning Agents: Go for 5052 alloy. Its higher magnesium content gives it excellent corrosion resistance.Marine/Saltwater Environments: 316 stainless steel might be better, but if sticking with aluminum, 5052-H32 or specialty alloys like 6061 offer better salt resistance than standard grades. Don't be shy – ask your tag supplier specifically about the alloy and its suitability for your exact conditions. Keywords matter: "corrosion-resistant aluminum tags," "chemical plant aluminum tags."
Mistake #2: Skipping the Prep Work (Surface = Everything)
You wouldn't paint a rusty, greasy door without sanding and cleaning it first, would you? Applying aluminum tags demands the same respect for the surface.
- The Problem: Tags applied to dirty, oily, rusty, wet, or improperly prepared surfaces simply won't stick reliably. Adhesives fail. Rivets or screws don't seat properly on uneven grime. The result? Tags falling off, getting lost, or becoming illegible as grime seeps underneath. It makes your whole labeling system look sloppy and unreliable.
- The Fix: PREP, PREP, PREP! This step is non-negotiable:Clean Thoroughly: Use an appropriate solvent (isopropyl alcohol is often a good start) to remove ALL oil, grease, dust, and loose particles. Degreasers are your friend.Dry Completely: No moisture allowed! Let the surface air dry or wipe it down with a clean, dry lint-free cloth.Roughen if Needed (For Adhesives): For very smooth surfaces (like polished metal or fiberglass), lightly scuffing the area with fine sandpaper can dramatically improve adhesive bond strength. Wipe away any dust afterward.Ensure Surface Compatibility: Verify the adhesive (if using) is rated for the material you're sticking it to (metal, plastic, painted surface, etc.). Using the right aluminum tags with the right prep guarantees they stay put.
Mistake #3: Going Cheap on the Engraving or Marking (Legibility is King)
What good is the toughest aluminum tag in the world if you can't read what's on it? Skimping on the marking quality is a false economy.
- The Problem: Shallow engraving, low-contrast stamping, or poorly printed information fades, fills with dirt, or becomes impossible to read under typical industrial lighting (or lack thereof). Think about a safety tag on a valve in a dimly lit basement, or an asset tag on a grimy piece of equipment. If the info isn't crystal clear and durable, the tag is useless.
- The Fix: INVEST IN PERMANENT, HIGH-CONTRAST MARKING:Deep Engraving: For ultimate durability, especially outdoors or in abrasive environments, deep engraving (using diamond drag or rotary engravers) is gold. Fill the grooves with durable enamel paint (like two-part epoxy paint) for maximum contrast. "Deep engraved aluminum tags" are a workhorse.Industrial-Grade Stamping: Properly done with hardened steel dies, stamping creates a permanent, recessed mark. Again, paint filling boosts visibility.Chemical Etching: Great for complex graphics or barcodes and very durable when done correctly.High-Performance Printing: If printing is necessary (e.g., for color coding or complex graphics), use UV-curable inks or specialized industrial coatings designed to withstand UV light, chemicals, and abrasion. Always prioritize contrast and depth! Ask: "Can this be easily read from a reasonable distance, by someone wearing gloves, in less-than-ideal light, five years from now?"
Mistake #4: Ignoring the Attachment Method (It's Got to Hold!)
So you've got the perfect alloy, prepped the surface like a champ, and have beautifully engraved info. But if the tag falls off, it's all for nothing. Choosing the wrong way to stick it on is a big league mistake.
- The Problem: Relying solely on a weak adhesive for a tag on a vibrating engine? Using tiny screws on a tag that needs to withstand impact? Trying to rivet a tag onto thin sheet metal that might warp? These are recipes for lost tags and failed identification.
- The Fix: MATCH THE ATTACHMENT TO THE APPLICATION & TAG SIZE:Industrial Adhesives: Fantastic for smooth, clean surfaces. BUT, know the limits! Use high-strength, permanent acrylic or epoxy-based adhesives specifically rated for metal and your environment (temperature, chemicals). Ensure the adhesive surface area is sufficient for the tag size. "High-temp adhesive aluminum tags" or "chemical-resistant adhesive tags" are specific solutions.Mechanical Fasteners (Rivets, Screws, Bolts): The go-to for extreme durability, vibration, impact resistance, or security. Choose the right fastener material (stainless steel is common) and size for the tag and the substrate thickness. Consider security fasteners (like tamper-proof rivets) if tampering is a concern. Always ensure the fastener holes in the aluminum tags are properly sized and reinforced if needed.Wire/Tie-Wraps: Useful for temporary tags or attaching to cables/hoses, but not generally suitable for permanent, high-integrity asset identification. Don't use them as a lazy permanent solution.Evaluate: Vibration? Heat? Impact risk? Tampering potential? Surface material? These factors dictate the best attachment method. Don't default to the cheapest or easiest option.
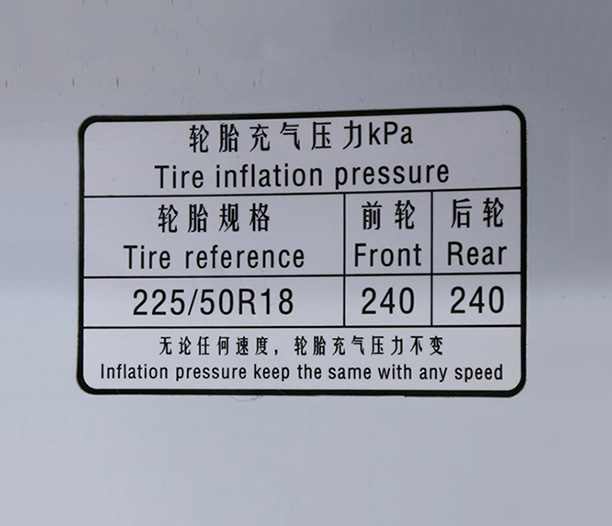
Mistake #5: Forgetting About the Long Game (Maintenance & Environment)
Aluminum tags are durable, but they aren't magical force fields. Ignoring their lifespan and environmental wear-and-tear is planning to fail.
- The Problem: Tags get covered in paint overspray during maintenance. Harsh solvents used for cleaning degrade markings or adhesives. Salt air slowly eats away at edges. UV radiation fades inks. Abrasion from people or materials brushing against them wears down the surface. Without considering these factors, your carefully chosen tags can become unreadable or detach prematurely.
- The Fix: PLAN FOR THE ENVIRONMENT & BUILD IN MAINTENANCE:Consider Protective Coatings: Clear, durable over-laminates (like polyester or polyurethane films) can shield engraved paint fills or printed information from UV fading, chemicals, and abrasion. Anodizing the aluminum tag itself provides a very hard, corrosion-resistant surface layer. "Laminated aluminum tags" or "anodized aluminum tags" offer extra protection.Location, Location, Location: Place tags where they are least likely to be damaged by routine operations, accidental bumps, spray, or high abrasion. Sometimes, a bracket or holder can position the tag more safely.The Maintenance Reality Check: If tags will get painted over (common in facilities), factor in a process for carefully masking them or plan for periodic replacement/cleaning as part of the maintenance schedule. Don't assume they'll survive unscathed.Regular Inspection: Make checking tag condition and legibility part of routine equipment inspections or safety audits. Catch problems before the information is lost or the tag fails.
Wrapping It Up: Get Smart With Your Aluminum Tags!
Look, aluminum tags are a fantastic, cost-effective solution for tons of industrial identification needs. But like any tool, you gotta use 'em right to get the best results and avoid wasting time and money. Dodging these five common mistakes – picking the wrong alloy, skipping surface prep, cheaping out on marking, using flimsy attachment, and ignoring the environment/maintenance – will put you miles ahead.
The key takeaway? Think it through. Consider the whole lifecycle of the tag and the specific demands of where it's going to live. Invest a little more time upfront in choosing the right specs and doing the prep properly. It pays off massively in long-lasting, reliable identification that keeps your operations safe, efficient, and well-organized. Don't just buy generic aluminum tags – buy the right aluminum tags, marked the right way, attached the right way, for the right job. Your future self (and your budget) will thank you! Now go label something properly!